Mining robots are drilling mines; they are performing blasting operations, producing and sorting ore. In their turn, automatic dumpers are autonomously transporting raw materials to a processing company. Some ten years ago, this kind of picture could be a script of a fiction movie. Today it is reality. The mining industry employs technologies enabling control of all processes, starting with setting tasks to a trucks fleet and up to controlling state of equipment. There are companies that have well succeeded in these matters, for example, Rio Tinto.
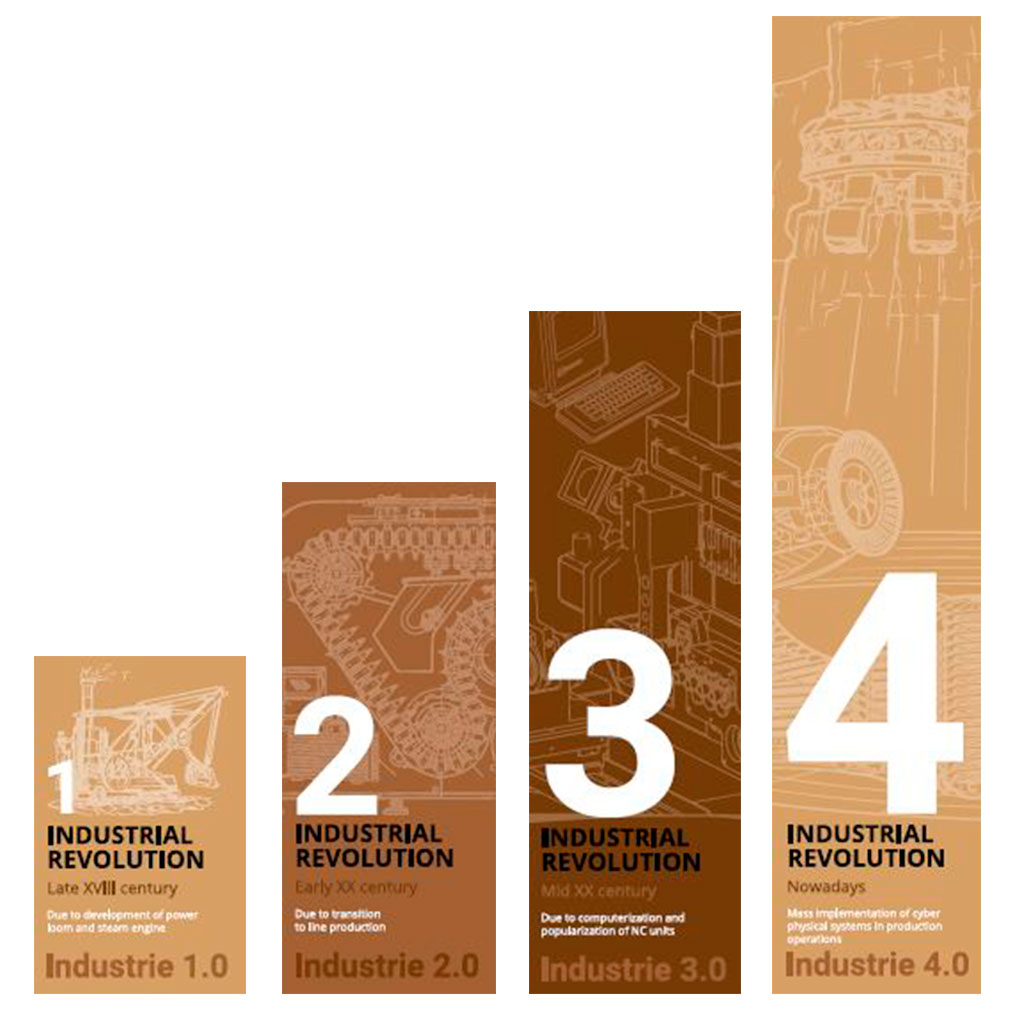
In 2008, the company launched the Mine of the Future program; thanks to this program the company became an operator of the largest in the world fleet of autonomous dumpers. These vehicles can move in complex conditions of a deposit under development without a driver and they are designed to transport 210 tons of useful load, mainly overburden. Today at three mines of Rio Tinto only, 69 of such trucks are in operation. Two years ago, the company tested drilling robots that prepare wells for loading a charge. Operators issue commands to the machines – so far it is them who choose sites for performing blasting operations. All the rest is performed by the machines: loading of explosives, site data collection, their transmission to the mater computer, etc. It is quite possible that Rio Tinto already uses robots at their facilities. By the end of the year 2018, the company plans to launch autonomous trains (without operators) for transportation of their goods in the Eastern Australia. Fleet of another Australian company – Fortescue Metals – includes 54 unmanned dumpers for ore transportation. Smart trucks have already transported about 240 million tons of commercial minerals or 75% of all cargoes of the company. In addition to that, Fortescue Metals has achieved a 20% increase in productivity.
BHP Billiton plans to use an automated ship for coal and iron ore transportation. According to initial estimates, autonomous ships will enable reduction of the annual expenses of the company by USD 86 million. Later on BHP Billiton plans to combine this trend with transportation of cargoes by autonomous trains.
Two years ago at the Tau Tona mine in South Africa a gold mining company – AngloGold Ashanti – tested new automatic drilling-andblasting systems, their usage helped to achieve new gold-bearing strata, development of which by traditional methods was not feasible due to process and economic reasons. Having appreciated a positive effect of the achieved results, management of the company decided to invest additional funds in further development and enhancement of this technology.
The list of high-technology companies can be continued further on. The trend is that mining companies try to minimize number of people in mines – ‘smart equipment’ enables significant improvement of safety and labor productivity. Focus on this kind of technologies can be traced not only in the mining sector but also in other industries.
According to German scientists, a new trend in industrial development signals the fourth industrial revolution. Why the fourth? The first one was in late XVIII – early XIX century and it referred to replacement of the muscle power of workers with the energy of steam and water in the first machines. Reasons for the second one were electrification and implementation of line production in early XX century. The third revolution was in 60–70s of the last century and it was conditioned by development of numeric control (NC) and microprocessors.
The fourth stage, according to German experts, shall be related to the internet and artificial intellect, to creation of ‘smart equipment’ and ‘smart plants’
Industrie 4.0 is the name of the ‘future project’ of the German federal government. It is a strategic plan for development of the German economy that provides for a breakthrough in information processing technologies. Germans have set a mission to network industrial equipment and entire production departments.
The initiative originating from Germany has resonated worldwide. In different countries, the concepts for implementation of Industrie 4.0 have been adopted: Industrie du Futur – in France, Manufacturing innovation 3.0 – in South Korea, Make in India – in India, Industria Conectada 4.0 – in Spain, The New Robot Strategy – in Japan, Manifattura Italia – in Italy. In the EU, there is a Factory of the future program, in US – Advanced manufacturing partnership. In Russia the National Technological Initiative was adopted, under this initiative 9 key markets are planned to be developed: AeroNet (air transport), AutoNet (highway transport), EnergyNet (powerengineering), FinNet (finances), FoodNet (food), HealthNet (medicine), MariNet (sea transport), NeuroNet (neurocommunications), SafeNet (safety).
Kazakhstan is also considering a possibility to pass to Industrie 4.0. The latest message of the President starts with an ‘historical challenge’ set up for Kazakhstan by the fourth industrial revolution, in the papers there are such topics as digitization, usage of additive technologies and robotic engineering. But to what extend are Kazakhstan companies ready to Industrie 4.0?
To answer this question Kazakhstan Industry Development Institute (subordinate company of the Ministry of Investment and Development of the RoK) together with foreign partners – Fraunhofer Applied Research Society and Swedish Trade and Export Council (Business Sweden) – are collecting information in different companies, including those of mining industry. The collected date will be analyzed; and then foreign experts will develop recommendations on implementation of elements of Industrie 4.0 in the Kazakhstan companies.
The questionnaire to survey companies of the mining sector was developed by the Swedish partners. As it was indicated in the reply of the Ministry of Investment and Development to our query, as of now information of 36 deposits out of 54 covered by the survey has been collected. These are deposits of such companies as Kazzinc, ERG, Kazminerals, Orken LLP (AMT), Voskhod-Oriel LLP, AK Altynalmas JSC, Temirtau Elecro Metallurgical Plant JSC, Kazakhsmys Corporation LLP. The information obtained based on the survey was sent to the Swedish experts for analysis.
In June of the current year a seminar for representatives of large mining companies of the RoK was held; during this meeting Swedish experts randomly interviewed participants of the event regarding implementation of elements of Industrie 4.0 at their companies. To assess state of the mining sector foreign partners visited Vasilkov deposit, ore mines of Altyntau Kokshetau JSC (Kazzink), Nurkazgan (Kazakhmys Corporation LLP) and Zholykbet deposits (Kazakhaltyn MMC JSC).
In July a meeting of large metallurgical companies (Kazzink, ERG, Kazakhmys, Kazminerals, ArcelorMittal, Altynalmas) and Ministry of Investment and Development was held; during this meeting the matters regarding plans and issues of companies concerning Industrie 4.0 were discussed.
As for the processing sector, the questionnaires and research methodology were developed by the Fraunhofer Institute. Representatives of the institute interviewed 30 different processing companies, as well as industry-specific associations.
Reply of the Ministry of Investment and Development states that ‘based on interviews and questionnaires it is planned to prepare a report on readiness of the processing industry sectors to implement elements of Industrie 4.0.’ Results of this work shall be presented in September of this year, meanwhile advanced technologies are introduced to the Kazakhstan entrepreneurs, visits of foreign mines are arranged, various presentations and discussions are held.
It is hard to say whether there are preconditions for the fourth industrial revolution in Kazakhstan nowadays. Whatever the case, studying the experience of implementation of the Industrie 4.0 project can be useful for those companies that focus on reaching modern European level. It is possible that robots will start to ‘beaver’ at our mines as well.